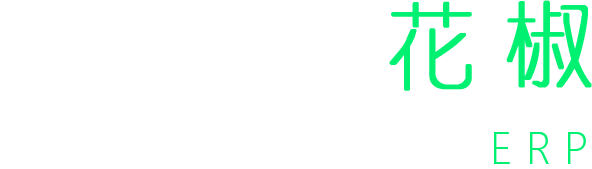
闭环供应链中的低效决策成本概念解析
闭环供应链(Closed-Loop Supply Chain, CLSC)是一种整合正向物流与逆向物流的系统,旨在通过回收、再制造、再利用等方式实现资源的循环利用。然而,在实际运作中,低效决策可能导致成本增加、效率降低,甚至影响企业的可持续发展。低效决策成本是指在闭环供应链中,由于决策不合理、信息不对称或执行不力而产生的额外成本。以下是该概念的核心要点:
1. 低效决策成本的主要来源
- 逆向物流管理不当
闭环供应链的核心是逆向物流,包括产品回收、检测、再制造等环节。如果回收流程设计不合理(如回收点分布不均、回收标准不明确),会导致物流成本增加、回收效率低下。 - 信息不对称
正向供应链与逆向供应链的信息共享不足,可能导致库存积压或短缺。例如,再制造产品的需求预测不准确,可能导致生产过剩或供应不足。 - 技术投入不足
闭环供应链需要先进的技术支持(如物联网、大数据分析)来优化回收和再制造流程。技术投入不足可能导致流程低效,增加人工成本和时间成本。 - 政策与法规风险
不同地区的环保法规差异较大,企业若未能及时调整策略,可能面临合规成本增加或市场准入受限的风险。
2. 低效决策成本的具体表现
- 运营成本增加
由于流程设计不合理或执行不力,可能导致运输成本、仓储成本、人工成本等增加。例如,回收产品未进行分类处理,导致再制造效率低下。 - 客户满意度下降
逆向物流的低效可能导致客户退货或换货周期延长,影响客户体验和品牌声誉。 - 资源浪费
再制造过程中若未能充分利用回收材料,可能导致资源浪费,增加原材料采购成本。 - 环境成本增加
低效决策可能导致废弃物处理不当,增加环境治理成本,甚至面临法律处罚。
3. 如何降低低效决策成本
- 优化逆向物流流程
通过合理布局回收点、制定明确的回收标准、引入自动化分拣技术等方式,提高回收效率。 - 加强信息共享
建立正向与逆向供应链的信息共享平台,实时监控库存、需求和回收情况,减少信息不对称。 - 技术投入与创新
利用物联网、大数据分析等技术优化回收和再制造流程,提高资源利用率和生产效率。 - 政策合规与风险管理
密切关注环保法规变化,及时调整供应链策略,确保合规运营,降低法律风险。
4. 案例分析
- 戴尔公司的闭环供应链
戴尔通过建立完善的逆向物流系统,实现了电脑和电子产品的回收与再利用。然而,若戴尔在回收点布局或再制造流程设计上存在低效决策,可能导致成本增加。例如,回收点分布过少可能导致客户退货不便,增加运输成本;再制造流程不优化可能导致生产周期延长,影响客户满意度。 - 汽车行业的再制造
汽车行业通过再制造发动机、变速箱等高价值零部件,实现了资源循环利用。然而,若再制造过程中的质量控制不严格,可能导致返工成本增加,甚至影响品牌声誉。
一、低效决策成本的主要来源
-
信息不对称
-
回收端与生产端数据不共享,导致再制造计划滞后或过量库存。
-
例如:无法实时获取废旧产品的数量、质量状态,延误再生产排期。
-
-
响应延迟
-
传统线性决策流程(如逐级审批)延长了逆向物流(退货、回收)的处理时间。
-
例如:退货商品因检测流程繁琐堆积,增加仓储成本。
-
-
技术工具缺失
-
缺乏IoT、区块链等技术支持,难以追踪产品全生命周期数据。
-
例如:手工记录回收品信息,错误率高且效率低。
-
-
协调失效
-
供应链各环节(回收商、再制造商、分销商)目标冲突,决策碎片化。
-
例如:回收商追求高回收量,而再制造商只需特定质量的旧件,导致无效运输。
-
二、低效决策成本的具体表现
成本类型 | 影响环节 | 典型场景 |
---|---|---|
库存积压成本 | 再制造环节 | 因预测不准导致回收件堆积,占用资金 |
运输冗余成本 | 逆向物流 | 低效路径规划增加空驶率 |
机会成本 | 全链条 | 延误再销售窗口期(如过季商品) |
质量损失成本 | 检测/分类环节 | 人工分拣错误导致可修复件被废弃 |
三、优化策略(降低决策成本)
-
数字化协同平台
-
部署供应链中台(如ERP+IoT),实现回收、生产、销售数据实时同步。
-
案例:华为通过区块链追溯旧手机部件状态,再制造决策效率提升40%。
-
-
动态决策模型
-
应用AI算法(如强化学习)动态调整回收定价、再生产计划。
-
示例:根据实时市场需求,自动匹配旧件拆解优先级。
-
-
流程再造
-
简化逆向物流审批层级,建立跨部门快速响应小组。
-
丰田的闭环供应链中,回收件检测时间缩短60%。
-
-
利益协调机制
-
设计收益共享合约(Revenue Sharing),统一各环节目标。
-
如:回收商按再制造商需求分类旧件,获得额外分成。
-
四、量化分析框架
通过决策成本系数(DCC)评估效率:
-
DCC>1 表明存在优化空间(如某家电企业DCC=1.8,通过引入AI分拣降至1.2)。
五、行业实践参考
-
Zara闭环时尚:RFID标签实时追踪旧衣回收,再制造决策周期从7天缩短至24小时。
-
CATL电池回收:基于大数据预测锂需求,动态调整拆解产能,库存成本降低35%。
通过技术赋能和流程重构,闭环供应链的决策成本可压缩30%~50%,直接提升再制造利润率(典型行业再制造利润增加5%~15%)。需根据企业实际数据建模细化方案。